Destylator przemysłowy to urządzenie, które służy do oddzielania składników mieszanin cieczy na podstawie różnicy w temperaturze wrzenia. Proces ten jest kluczowy w wielu gałęziach przemysłu, w tym w przemyśle chemicznym, petrochemicznym oraz spożywczym. W destylacji wykorzystuje się zasadę, że różne substancje mają różne temperatury wrzenia, co pozwala na ich skuteczne rozdzielenie. W praktyce oznacza to, że ciecz podgrzewana jest do momentu, gdy jedna z jej frakcji zaczyna parować. Para ta następnie przechodzi przez chłodnicę, gdzie skrapla się i zbiera jako oddzielny produkt. Destylatory przemysłowe mogą być wykorzystywane do produkcji alkoholu, oczyszczania wody, a także do separacji różnych chemikaliów. W zależności od potrzeb, destylatory mogą mieć różne konstrukcje i rozmiary, od małych jednostek laboratoryjnych po ogromne kolumny destylacyjne stosowane w dużych zakładach produkcyjnych.
Jakie są rodzaje destylatorów przemysłowych i ich funkcje
W przemyśle wyróżnia się kilka rodzajów destylatorów, które różnią się konstrukcją oraz zastosowaniem. Najpopularniejsze z nich to destylatory prostokątne oraz kolumnowe. Destylatory prostokątne charakteryzują się prostą budową i są często wykorzystywane w mniejszych zakładach produkcyjnych lub laboratoriach. Z kolei destylatory kolumnowe są bardziej skomplikowane i efektywne, co czyni je idealnymi do dużych operacji przemysłowych. Wśród innych typów można wymienić również destylatory frakcyjne, które pozwalają na rozdzielenie kilku składników o zbliżonych temperaturach wrzenia. Każdy z tych typów ma swoje unikalne cechy i zastosowania, co sprawia, że wybór odpowiedniego urządzenia zależy od specyfiki procesu produkcyjnego oraz rodzaju przetwarzanych substancji. Dodatkowo istnieją również destylatory próżniowe, które działają w obniżonym ciśnieniu, co pozwala na destylację substancji w niższych temperaturach.
Jakie materiały są używane do budowy destylatorów przemysłowych
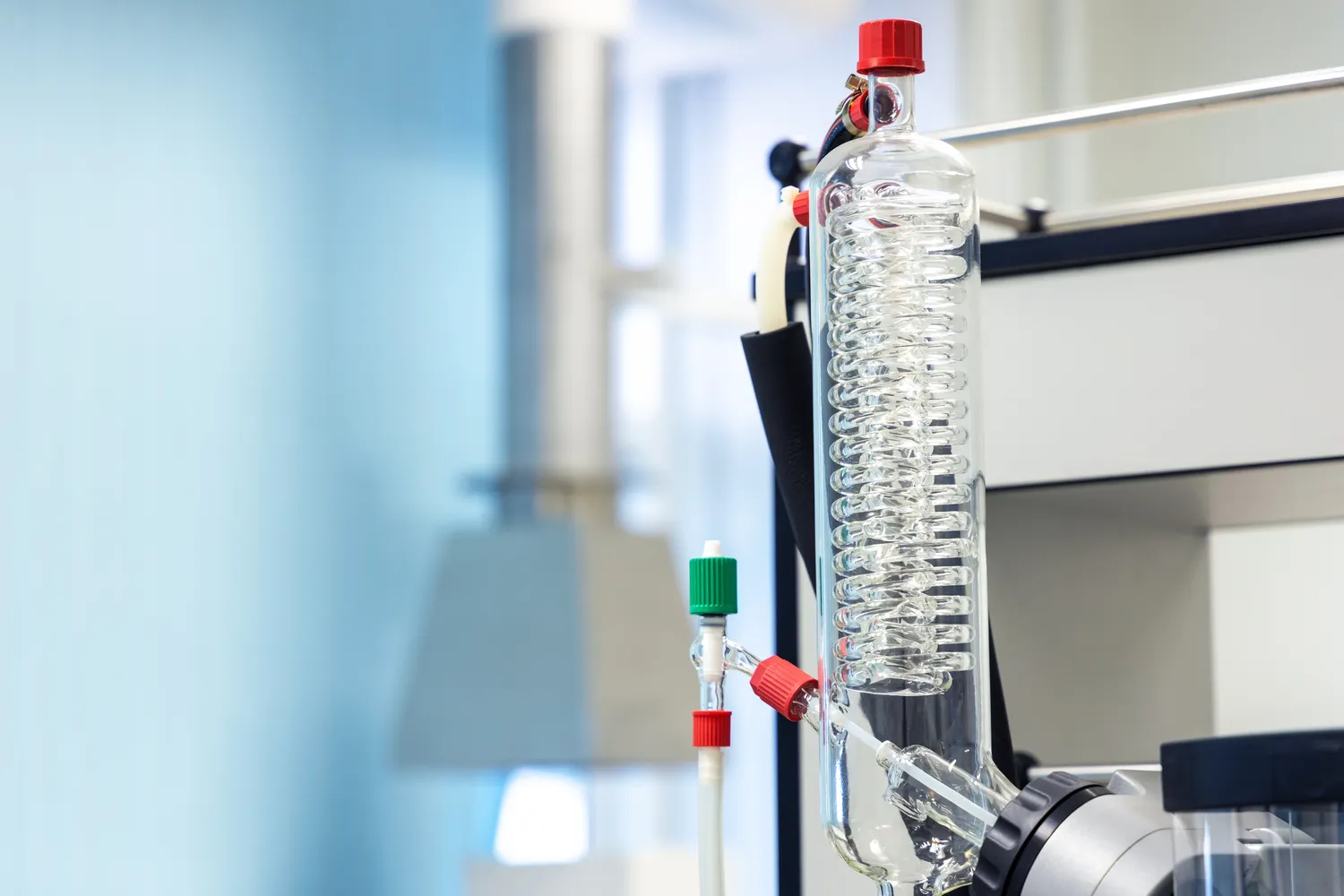
Budowa destylatora przemysłowego wymaga zastosowania materiałów odpornych na wysokie temperatury oraz korozję. Najczęściej wykorzystywanym materiałem jest stal nierdzewna, która charakteryzuje się wysoką odpornością na działanie chemikaliów oraz wysoką trwałością mechaniczną. Stal nierdzewna jest idealnym wyborem dla większości procesów destylacyjnych ze względu na swoje właściwości higieniczne oraz łatwość w utrzymaniu czystości. W niektórych przypadkach stosuje się również materiały takie jak miedź czy szkło borokrzemowe, zwłaszcza w mniejszych instalacjach laboratoryjnych lub przy produkcji alkoholu rzemieślniczego. Miedź ma dodatkową zaletę polegającą na tym, że neutralizuje niepożądane związki siarki podczas procesu fermentacji. W przypadku bardziej zaawansowanych technologii można spotkać także kompozyty czy materiały ceramiczne, które oferują jeszcze wyższą odporność na ekstremalne warunki pracy.
Jakie są najważniejsze zalety stosowania destylatorów przemysłowych
Stosowanie destylatorów przemysłowych przynosi wiele korzyści zarówno dla producentów, jak i dla końcowych użytkowników produktów. Przede wszystkim umożliwia efektywne rozdzielanie składników chemicznych oraz uzyskiwanie wysokiej czystości produktów końcowych. Dzięki temu procesy produkcyjne stają się bardziej wydajne i opłacalne. Kolejną istotną zaletą jest możliwość przetwarzania dużych ilości surowców w krótkim czasie, co znacząco zwiększa wydajność zakładów przemysłowych. Destylatory pozwalają również na recykling surowców poprzez ich ponowne wykorzystanie po procesie separacji. Dodatkowo nowoczesne systemy destylacyjne są często wyposażone w technologie automatyzacji i monitorowania procesów, co zwiększa bezpieczeństwo pracy oraz minimalizuje ryzyko błędów ludzkich.
Jakie są najnowsze technologie w destylacji przemysłowej
W ostatnich latach rozwój technologii destylacyjnych przeszedł znaczną ewolucję, co przyczyniło się do zwiększenia efektywności i wydajności procesów przemysłowych. Nowoczesne destylatory wykorzystują zaawansowane systemy automatyzacji, które pozwalają na precyzyjne kontrolowanie parametrów pracy, takich jak temperatura, ciśnienie czy przepływ cieczy. Dzięki temu możliwe jest uzyskanie lepszej jakości produktów oraz minimalizacja strat surowców. Wprowadzenie technologii cyfrowych i Internetu Rzeczy (IoT) umożliwia zdalne monitorowanie i zarządzanie procesami destylacyjnymi, co zwiększa elastyczność produkcji i pozwala na szybsze reagowanie na zmieniające się warunki rynkowe. Kolejnym istotnym trendem jest zastosowanie energii odnawialnej w procesach destylacyjnych, co przyczynia się do zmniejszenia śladu węglowego i obniżenia kosztów operacyjnych. Przykładem mogą być systemy wykorzystujące energię słoneczną do podgrzewania cieczy w procesie destylacji.
Jakie są wyzwania związane z użytkowaniem destylatorów przemysłowych
Pomimo licznych zalet, użytkowanie destylatorów przemysłowych wiąże się również z pewnymi wyzwaniami. Jednym z głównych problemów jest konieczność regularnego utrzymania i konserwacji urządzeń, aby zapewnić ich prawidłowe działanie oraz uniknąć awarii. Wysoka temperatura oraz ciśnienie robocze mogą prowadzić do zużycia materiałów, co wymaga częstych przeglądów technicznych. Kolejnym wyzwaniem jest zarządzanie odpadami powstającymi w wyniku procesu destylacji. Wiele substancji chemicznych może być toksycznych lub szkodliwych dla środowiska, dlatego konieczne jest wdrażanie odpowiednich procedur ich utylizacji. Dodatkowo, w miarę rosnących wymagań dotyczących jakości produktów oraz norm środowiskowych, przedsiębiorstwa muszą inwestować w nowoczesne technologie oraz szkolenia pracowników, co generuje dodatkowe koszty.
Jakie są koszty związane z zakupem i eksploatacją destylatorów przemysłowych
Koszt zakupu destylatora przemysłowego może znacznie się różnić w zależności od jego rodzaju, wielkości oraz specyfikacji technicznych. Proste jednostki laboratoryjne mogą kosztować kilka tysięcy złotych, podczas gdy zaawansowane kolumny destylacyjne stosowane w dużych zakładach produkcyjnych mogą osiągać ceny rzędu milionów złotych. Oprócz kosztu zakupu należy uwzględnić także wydatki związane z instalacją oraz uruchomieniem urządzenia. Koszty eksploatacyjne obejmują zużycie energii elektrycznej oraz mediów grzewczych, a także koszty związane z konserwacją i naprawami. Warto również pamiętać o kosztach surowców wykorzystywanych w procesie destylacji oraz ewentualnych opłatach za utylizację odpadów. W dłuższej perspektywie czasowej inwestycja w nowoczesne technologie może przynieść oszczędności dzięki zwiększonej efektywności energetycznej oraz lepszej jakości produktów końcowych.
Jakie są kluczowe czynniki wpływające na wybór odpowiedniego destylatora przemysłowego
Wybór odpowiedniego destylatora przemysłowego to kluczowa decyzja, która może znacząco wpłynąć na efektywność procesu produkcyjnego. Istotnym czynnikiem jest rodzaj przetwarzanych substancji oraz ich właściwości fizykochemiczne, takie jak temperatura wrzenia czy lepkość. Należy również uwzględnić wymagania dotyczące jakości produktów końcowych oraz normy regulacyjne obowiązujące w danej branży. Kolejnym aspektem jest skala produkcji – małe zakłady mogą potrzebować prostszych rozwiązań, podczas gdy duże przedsiębiorstwa często korzystają z bardziej zaawansowanych technologii kolumnowych. Ważne jest także rozważenie kosztów zakupu oraz eksploatacji urządzenia, które powinny być zgodne z budżetem firmy oraz jej strategią rozwoju.
Jakie są przyszłe kierunki rozwoju technologii destylacyjnej
Przyszłość technologii destylacyjnej zapowiada się obiecująco dzięki ciągłemu rozwojowi innowacyjnych rozwiązań i metod produkcji. Wśród najważniejszych trendów można wymienić dalszą automatyzację procesów oraz integrację systemów informatycznych z urządzeniami przemysłowymi. Dzięki temu możliwe będzie jeszcze lepsze monitorowanie parametrów pracy oraz optymalizacja procesów produkcyjnych w czasie rzeczywistym. Zwiększona świadomość ekologiczna społeczeństwa sprawia, że przedsiębiorstwa będą coraz bardziej skłonne do inwestowania w technologie przyjazne dla środowiska, takie jak systemy odzysku ciepła czy wykorzystanie energii odnawialnej w procesach destylacyjnych. Ponadto rozwijają się badania nad nowymi materiałami konstrukcyjnymi, które mogą poprawić efektywność energetyczną urządzeń oraz ich odporność na korozję i wysokie temperatury.
Jakie są kluczowe aspekty bezpieczeństwa w pracy z destylatorami przemysłowymi
Bezpieczeństwo w pracy z destylatorami przemysłowymi jest niezwykle istotnym zagadnieniem, które wymaga szczególnej uwagi ze strony pracodawców oraz pracowników. Przede wszystkim, każde urządzenie powinno być zgodne z obowiązującymi normami i przepisami dotyczącymi bezpieczeństwa, co obejmuje zarówno konstrukcję, jak i eksploatację. Kluczowym elementem jest regularne przeprowadzanie przeglądów technicznych oraz konserwacji, aby zminimalizować ryzyko awarii. Warto również wdrożyć odpowiednie procedury operacyjne, które będą regulować sposób obsługi destylatora oraz postępowania w przypadku awarii. Szkolenie pracowników w zakresie obsługi urządzeń oraz zasad bezpieczeństwa jest niezbędne dla zapewnienia bezpiecznego środowiska pracy. Dodatkowo, stosowanie odpowiednich środków ochrony osobistej, takich jak rękawice czy gogle ochronne, może znacząco zmniejszyć ryzyko urazów.